Understanding the Art of Welding: How to Avoid Undercut Welding Issues for Flawless Construction Outcomes
Efficiency and precision are paramount in the world of welding, where even the slightest flaw can compromise the structural integrity of a fabricated item. One typical challenge that welders face is damaging, a problem that can damage a weld joint and lead to costly rework. By comprehending the origin causes of undercut welding and implementing efficient techniques to prevent it, welders can boost their craft to new degrees of quality (Preventing weld undercut). In the quest of remarkable construction outcomes, mastering the art of welding to avoid undercut issues is not simply an ability however a requirement for those pursuing excellence in their work.
Understanding Undercut Welding

To avoid undercut welding, welders ought to ensure appropriate welding specifications, such as changing the current, voltage, travel speed, and preserving the proper electrode angle. Additionally, utilizing the ideal welding method for the details joint configuration is vital. Using weaving motions or backstepping strategies can help guarantee appropriate weld steel deposition and reduce the chance of undercut formation. Normal evaluation of welds throughout and after the welding procedure is additionally important to capture any undercut early and make required modifications to avoid more problems. Preventing weld undercut. By comprehending the causes of undercut welding and executing safety nets, welders can attain top notch, structurally audio welds.
Root Causes Of Undercut in Welding
Comprehending the aspects that add to damage in welding is crucial for welders to produce high-quality, structurally audio welds. When the weld metal does not correctly fill the groove formed in between the base steel and the formerly transferred weld steel, undercutting takes place. Numerous elements can cause damage in welding. One usual reason is too much warm input. Welding at high temperature levels for extended durations can lead to the base metal thawing greater than desired, leading to damage. Inadequate welding existing or inaccurate welding speed can additionally add to undercut. Inadequate current may not give sufficient heat to thaw the base and filler metals sufficiently, while extreme speed can protect against appropriate blend, triggering undercut. Additionally, incorrect electrode angles or incorrect lantern manipulation methods can create areas of reduced weld metal deposition, advertising undercut. Understanding these reasons and implementing appropriate welding strategies can assist protect against undercutting concerns, guaranteeing long lasting and solid welds.
Techniques to Avoid Undercutting

To mitigate the risk of undercutting in welding, welders can utilize critical welding strategies aimed at boosting the high quality and stability of the weld joints. One reliable approach is to adjust the welding parameters, such as voltage, current, and travel speed, to guarantee appropriate warm input and deposition. Keeping an ideal electrode angle and making certain regular traveling rate can additionally aid protect against undercut. In addition, making use of the proper welding strategy for the certain joint arrangement, such as weave or stringer grains, can add to minimizing undercutting. Preventing weld undercut.
Moreover, appropriate joint preparation, consisting of making certain clean base materials devoid of impurities and utilizing the suitable welding consumables, is crucial in preventing undercut flaws. Utilizing back-step welding techniques and regulating the weld bead account can likewise help disperse warm evenly and lessen the risk of undercut. Normal assessment of the weld joint during and after welding, along with executing quality guarantee measures, can assist in attending to and spotting damaging issues without delay. By executing these strategies vigilantly, welders can attain flawless manufacture results with minimal undercut flaws.
Significance of Appropriate Welding Criteria
Selecting and maintaining proper welding why not try here criteria is essential for achieving successful welds with marginal defects. Welding parameters refer to variables such as voltage, present, take a trip speed, electrode angle, and securing gas flow rate that directly impact the welding process. These specifications should be very carefully readjusted based upon the kind of product being bonded, its density, and the welding strategy used.
Correct welding criteria ensure the correct amount of heat is applied to thaw the base steels and filler product evenly. If the criteria are established too expensive, it can cause extreme warm input, triggering distortion, burn-through, or spatter. On the other hand, if the criteria are also reduced, incomplete fusion, lack of infiltration, or damaging may occur.
Quality Control in Welding Workflow
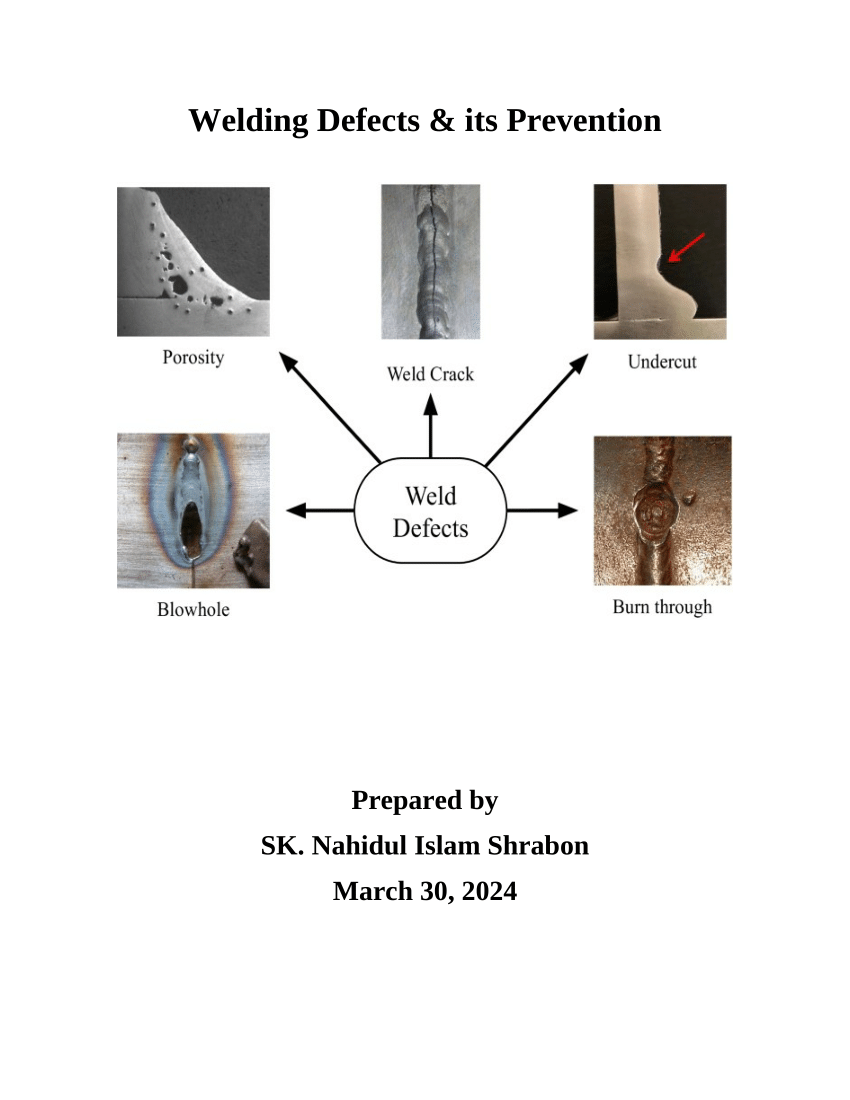
Verdict
Finally, grasping the art of welding requires a detailed understanding of undercut welding, its reasons, and Your Domain Name techniques to stop it. By making sure appropriate welding parameters and carrying out quality control methods, flawless construction results can be attained. It is important for welders to consistently pursue excellence in their welding operations to avoid undercut issues and generate high-quality welds.
Undercut welding, a common flaw in welding procedures, occurs when the weld metal doesn't effectively load the groove and leaves a groove or anxiety along the bonded joint.To avoid undercut welding, welders ought to ensure correct welding criteria, such as changing the existing, voltage, traveling rate, and keeping the proper electrode angle. Insufficient welding existing or inaccurate welding rate can additionally contribute to damage.To minimize the danger of undercutting in welding, welders can use critical welding strategies aimed at improving the high quality and integrity of the weld joints.In conclusion, grasping the art of welding calls for an extensive understanding of undercut welding, its causes, and techniques to stop it.